spray for testing seal welds|seal welding procedure : convenience store Using a weld sealant is less costly than pressurizing a system to detect the porosity leaks and provides the added protection of corrosion prevention. Experienced fire protection professionals agree, Don’t risk it – wick it! webToday's online casino slots and video slots function the same way. The only distinction is that the complex, spring-loaded automatic mechanism has been swapped by computer .
{plog:ftitle_list}
web28 de set. de 2022 · Een goede sport bh is voor iedere hardlopende vrouw een must. .
Current US MIL-STD-883 Test Method 1014 significantly tightened the leak rate requirements for all sizes of hermetic packages with failure criteria now expressed in air with rates as low as 1E-9 atm-cm 3 /sec (air). Penetrant inspection is a simple and effective method for locating surface cracks and flaws in the field after welding. In addition, this is one of the most popular Nondestructive Examination (NDE) methods in the industry.
In the mechanical and structural fields, seal welds are used most often not to prevent leakage out of a container, but to pre-vent entry of a fluid into a space where some type of harmful .
Bursting Strength Tester distributor
Using a weld sealant is less costly than pressurizing a system to detect the porosity leaks and provides the added protection of corrosion prevention. Experienced fire protection professionals agree, Don’t risk it – wick it!Product Details. Visible dye penetrant testing kits include precleaner, visible red dye, and a solvent-based developer to indicate cracks, pitting, and porosity. Looking for MAGNAFLUX, Aerosol Can, SK-816 Spotcheck Kit? Find it at . When it comes to testing a welding crack, there are three main non-destructive testing (NDT) methods to consider: Liquid Penetrant Testing (PT), Magnetic Particle Testing . What Exactly is Seal Welding? Seal welding plays a pivotal role in various industries, ensuring that connections remain air-tight and water-tight. By design, these welds resist leakages, preventing fluids (be it gaseous or liquid) .
Seal welds have been designed to form a leakproof tight seal between metal components. Seal welds are designed to prevent any gas or liquid leakage. Seal welds are crucial in applications that require a complete seal, .
weld inspection procedures
Seal Welds: A seal weld is used to prevent the inflow of fluid causing corrosion and prevent the infiltration of oxygen-laden air and moisture. Galvanized parts specify seal welds to prevent .“Seal Welds” Practical Ideas for the Design Professional by Duane K. Miller, Sc.D., P.E. Design File Introduction What is a “seal weld?”AWS A3.0, Standard Welding Terms and Definitions, defines a seal weld as: “Any weld designed primarily to provide a specific degree of tight-ness against leakage.” The purpose of a seal weld may
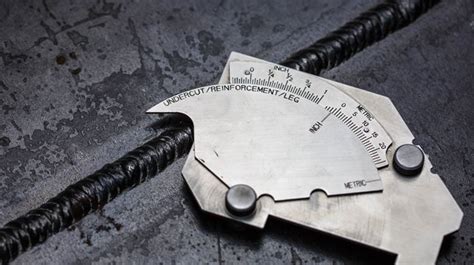
When it comes to testing a welding crack, there are three main non-destructive testing (NDT) methods to consider: Liquid Penetrant Testing (PT), Magnetic Particle Testing (MT), and Eddy Current Testing (ET). Liquid Penetrant Testing involves applying a liquid dye to the weld surface and then removing the excess to reveal any cracks that may .“Seal Welds” Practical Ideas for the Design Professional by Duane K. Miller, Sc.D., P.E. . ultrasonic testing (UT) of such connections. Consider Figure 4 in which a CJP groove weld with steel backing is inspected with UT. An alternate sound path is created when the seal welds are placed around the left-in-place backing. Such implications .
If you've ever welded stainless steel, you know that heat tint is a very common occurrence.Heat tint appears as a discoloration and can take on a stunning "rainbow" appearance, as shown in these photos. The discoloration that you see is actuallyan oxide layer whose color is related to the temperature reached during the welding process -- .
2.1.5 Types of Welds. Seal Welds: A seal weld is used to prevent the inflow of fluid causing corrosion and prevent the infiltration of oxygen-laden air and moisture. . Damage during welding should be repaired using a zinc-rich paint or thermal spray zinc coating to restore corrosion protection. Inspection: Welded joints should be inspected .What is Thermal Spray Welding? Thermal spray welding (thermal spraying or metalizing) is a coating process used to apply materials onto a substrate.It improves or modifies its surface properties. Thermal spray welding involves spraying molten or semi-molten materials onto a prepared surface, not like traditional welding processes where materials are fused at high .
Seal welding is used to create a watertight or airtight connection between two pieces of metal. This type of welding is often used in the construction of boats, pipelines, and pressure vessels.. Seal welding can be performed using various types of welding processes, including gas tungsten arc welding (GTAW), plasma arc welding (PAW), and electron beam .
It is used to remove any high-temperature scale/ oxides & nearby low chrome from steel surface by the chemical application after welding. Pickling is an efficient process for the removal of scale, dirt, and oxides from materials. The scale that is removed results from hot forming, welding, or heat treating operations and from corrosion. Seal welding in tube-to-tube sheet joints is critical because any leaks could lead to a loss of efficiency or performance in the heat exchanger, or potentially cause safety hazards. . ultrasonic testing, or dye penetrant testing may be used to verify the quality and integrity of the seam weld. Overall, the goal of a seam weld is to create a . The Comprehensive Guide to Anti-Spatter Sprays in Welding: Types, Benefits, and Application Introduction: Welding projects often encounter the challenge of spatter – those pesky droplets that can adhere to surfaces and equipment, making cleanup a daunting task. . How should anti-spatter spray be applied for maximum effectiveness? Follow the .
The plasma spray welding process has the greatest amount of versatility. Here, gas is used (hydrogen, helium, nitrogen, argon) with an electric arc ionizing the gas. The process operates at over 10,000C, which is hotter than the melting point for metals. The powder is injected into the flame, melted, and moved to the material being sprayed.welds. Regardless of the differences between test meth-ods, all testing procedures measure either a composite average or a “weak-link” component of the property of interest within the area sampled. Thus, an understand-ing of the test details is necessary to interpret the results. When testing a welded or brazed joint, the investiga-
Auto Pneumatic Bursting Strength Tester distributor
test is considered unacceptable. Other validation tests include a 2 hour Salt Spray or 24 hour high-humidity test.These tests are performed by placing passivated parts in a highly controlled chamber which creates an accelerated corrosive environment. After subjecting the test pieces to the corrosive atmosphere for the prescribed exposure Penetrant inspection is a simple and effective method for locating surface cracks and flaws in the field after welding. In addition, this is one of the most popular Nondestructive Examination (NDE) methods in the industry. . For example, the American Society for Nondestructive Testing (ASNT) uses the term liquid penetrant testing (PT . ASME B31.3: Visual Inspection Acceptance Criteria for Welds is given in Table 341.3.2. API 1104: Acceptance criteria given in Clause 8: Inspection & Testing of Welds. ISO 5817: Acceptance criteria given in Table 1 .Leak Testing - TQC's beginners and fundamentals guide to helium leak testing, what is it, why use it and the benefits of helium leak testing. . One can also either sniff or spray helium. . it would be good to try and insert some .

If cold crack repairs using pins or plugs are not sufficient, welding is another option for repairing cracks in engine castings. Furnace welding, flame spray welding, or TIG welding can be employed depending on the type of .Non-destructive testing (NDT) methods shall be selected in accordance with EN 12062 by personnel qualified according to Level 3 as defined in EN 473. Generally ultrasonic testing or radiographic testing applies to butt welds and penetrant testing or magnetic particle inspection applies to fillet welds.
seal welding techniques pdf
seal welding requirements
Spray welding, also known as flame spraying, is a welding process that involves spraying molten metal or wire particles onto a surface to create a bond. In spray welding, a wire or powder feedstock is melted by a flame or plasma torch and sprayed onto a prepared surface, forming a coating or build-up layer. .Welding procedure test. Arc and gas welding of steels and arc welding of nickel and nickel alloys, BSI; ↑ 6.0 6.1 6.2 BS EN ISO 14555:2017, Welding. Arc stud welding of metallic materials, BSI; ↑ 7.0 7.1 7.2 BS EN 1011-2:2001, Welding. Recommendations for welding of metallic materials. Arc welding of ferritic steels, BSI; ↑ BS EN 1011-1: . Gas Weld Testing. Inspection weld quality testing criteria for gas welds: The weld should be of consistent width throughout. The two edges should form straight parallel lines. The face of the weld should be slightly convex with a reinforcement of not more than 1/16 in. (1.6 mm) above the plate surface. HYDROGEN LEAK DETECTION SPRAY. . Whichever method is used, Stein Seal Industrial performs all of its hydrogen seal testing to industry-established standards and best practices. Every Stein-built hydrogen seal can be relied upon to provide safe and effective performance over a long service life. . • NADCAP Welding • FAA Repair Station .

Computer system control Elmendorf Tearing Tester distributor
In the world of non-destructive testing (NDT), dye penetrant testing is a widely employed method for detecting surface-breaking defects in various materials, including metals, plastics, and ceramics. This technique, often referred to as liquid penetrant inspection or simply penetrant testing, plays a crucial role in ensuring the structural integrity and safety of a wide range of .Reveal imperfections both at and slightly below the surface of your metal part, unlike other flaw detection methods. Use these particles with a magnetic yoke to check for faulty seams, welding defects, and fatigue cracks to make sure metal parts will be safe under high stress. The yoke creates a magnetic field that draws the particles towards flaws, making them easy to spot. Two austenitic stainless steel (ASS) plates, 304L and 316L, were cold-rolled (304R and 316R) with a 10% reduction in thickness and then subjected to laser welding. Cold rolling caused slight surface hardening and introduced residual tensile stress into the ASS plates. The susceptibility to stress corrosion cracking (SCC) of the welds (304RW and 316RW) was .
3. X-Ray Testing. This physical weld testing radiographic method reveals the presence and nature of the internal defects in a sample of the weld, like cracks, blowholes, slag, and improper fusion zones. We keep an x-ray tube on one side of the sample welded plate and an x-ray film specially designed sensitive emulsion on the other side.which the expansion, welding and testing is done. One camp says to weld, test the weld and then expand; another says expand, weld and then test the weld. The purchaser must ultimately make the decision for which sequence to use. Figure 9 lists the steps to follow if "weld tube ends-and then expand" is chosen as the attachment method.
seal welding purpose
Encontre jogos infantis educativos e divertidos para bebês e crianças de 3, 4 ou 5 anos, totalmente online e grátis. Escolha entre jogos de colorir, pintar, quebra cabeça, carros, slime, Paw Patrol, Hello Kitty e muito mais.
spray for testing seal welds|seal welding procedure